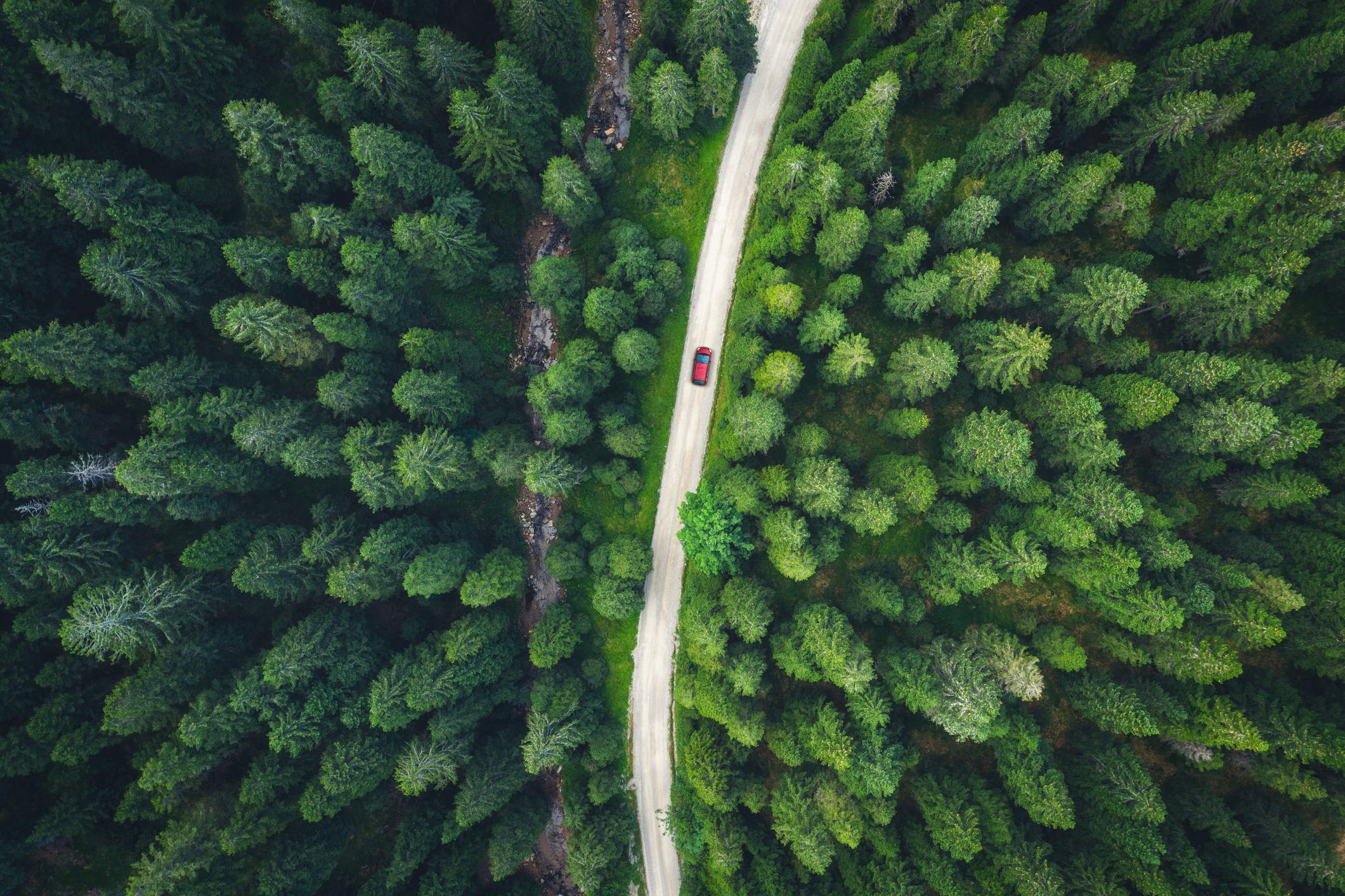
Environmental issues closely related to the automotive industry
Vehicle manufacturers have developed various technologies to reduce CO2 emissions, introducing hybrid vehicles (HVs) and plug-in hybrid vehicles (PHVs) to the market. However, according to the FY2020 Greenhouse Gas Emissions (Preliminary Figures) published by the Ministry of the Environment(*1), 17.7% of the total CO2 emissions in Japan in 2019 came from the transportation sector, and most of these emissions were from vehicles. Given this, vehicles significantly impact global warming, and more efforts are needed to reduce CO2 emissions further.
Of course, Japan is not alone in this trend. Globally, the most stringent regulations are in Europe, which set a target of 95g of CO2 emissions per kilometer driven by vehicles in 2021, aiming to reduce CO2 emissions to around 70 g/km by 2025. The subsequent most stringent regulation is in the United States, which has set a target of 89 g/km by 2025.
In Asia, Japan, China, and India have been working on CO2 emission regulations, targeting 114 g/km by 2020, 116 g/km by 2020, and 113 g/km by 2021 respectively.
Automotive Industry Initiatives to Reduce CO2 Emissions
The Development of EVs and HVs
One of the most symbolic initiatives is the development of EVs and HVs. HVs have already become popular worldwide, with many users choosing HVs for their low fuel consumption and quietness in everything from light cars to large vehicles. EVs, which are even more environmentally friendly than HVs, are also attracting increasing attention and are being introduced one after another to the market.
EVs, which do not emit CO2 while driving, are the ideal form of eco-car. However, the short cruising range of EVs compared to gasoline-powered vehicles and HVs has become an issue, requiring higher battery performance and a lighter vehicle body.
Improved fuel economy of gasoline-powered vehicles
While the need for EVs and HVs is rapidly expanding, gasoline-powered vehicles with relatively low body prices also enjoy strong popularity. Many gasoline-powered cars, especially minicars and compact cars, are as fuel-efficient as HVs, with significantly lower CO2 emissions.
In addition, large vehicles such as minivans and SUVs have generally had large engines with large displacements. Still, recently the trend has been toward engine downsizing, resulting in lower fuel consumption.
Facilitation of transportation infrastructure using AI and IoT
It is essential not only to develop technologies for vehicles themselves but also to facilitate transportation infrastructure to reduce overall CO2 emissions. For example, when heavy traffic congestion occurs daily, long periods of idling result in unnecessary CO2 emissions.
To solve such chronic traffic congestion, systems that facilitate traffic infrastructure by utilizing cutting-edge technologies such as AI and IoT are attracting attention. Suppose machine learning can predict the sections where traffic jams will occur. In that case, it will be possible to select routes that avoid them, easing traffic congestion while contributing to CO2 emissions reduction.
*1 https://www.pwc.com/jp/ja/knowledge/thoughtleadership/automotive-insight/vol4.html
Technologies and methods to improve vehicle fuel efficiency
The key to reducing CO2 emissions is how efficiently a vehicle can run on less fuel, in other words, how fuel-efficient it can be. In many cases, designers review the materials and design of the vehicle engine and the entire car to achieve greater efficiency.
Below are five common examples of the technologies and methods used to make vehicles more fuel-efficient.
Weight reduction of the vehicle body can be achieved by reviewing the structure and eliminating unnecessary parts and sections while ensuring the rigidity of the vehicle body. Weight reduction can also be achieved by changing to lighter materials for the same shape and size.(*2)Engine Improvement. Energy not converted into power during combustion can be reduced by changing ignition technologies or fuel injection methods to improve engine combustion efficiency. A turbocharger feeds highly compressed air into the engine and can obtain more power with less displacement.Drive system improvement. Energy loss from the engine can be suppressed by reducing the friction coefficient of the drive shaft. Reducing rpm changes through AT multi-step improves combustion efficiency. Continuously Variable Transmissions (CVT) have less energy loss than ATs, thus improving fuel efficiency.The reduction of rolling resistance friction can be reduced by reviewing the tire surface shape (tread pattern) to achieve lower fuel consumption.The reduction of air resistance. Improved body shape based on fluid dynamics reduces air resistance during driving, resulting in lower fuel consumption.
*2 MLIT HP http://www.mlit.go.jp/common/001225519.pdf
Material selection and the introduction of manufacturing methods to further accelerate vehicle weight reduction
Among these, weight reduction of the car body is vital to lower fuel consumption. Materials and manufacturing methods are the key to reducing size and weight while maintaining the strength of each part. Below are three specific examples of material selection and manufacturing methods requirements.
Shift from high-tensile steel to aluminum and then to magnesium
Steel has long been used as a structural material for vehicles due to its superior strength, formability, surface treatment, and price. High-tensile and ultra-high-tensile steel sheets add materials such as carbon, nickel, silicon, manganese, and other elements in minimal quantities to increase strength. Furthermore, these materials utilize microstructure control, which allows the materials to be used for structural parts, such as vehicle center pillars, front pillars, side roof rails, and front roof rails, in thinner and more lightweight configurations.
While high-tensile and ultra-high tensile steel have traditionally been used for automotive frame members, aluminum—even lighter than steel—is increasingly popular for engine components such as cylinders and exterior panels such as bumper beams, doors, and roofs.
And now, magnesium—the lightest of all practical metals—is also expanding. Magnesium's strength and reliability have led to widespread use in aerospace. Among automotive parts, engineers often specify magnesium for use in fuel tanks, transmissions, brackets, and seat frames.
Magnesium is even lighter than aluminum; switching from aluminum to magnesium could reduce the weight of components by a quarter to a third. Incidentally, magnesium originally had drawbacks such as high flammability and being prone to corrosion. Still, engineers have overcome these drawbacks by developing magnesium alloys that combine metals such as aluminum and zinc.
Utilizing lightweight resin materials
At the same time, there is a marked trend toward replacing metal materials such as high-tensile-strength steel, aluminum, and magnesium with lighter-weight resins. The Mitsubishi Chemical Group has developed high-performance resin materials and is contributing to the weight reduction of vehicles by replacing metals with resin for interior parts. Resin materials are already being used mainly in instrument panel cores, interior parts, and motor housings, functional parts. In addition, the use of unique fiber-reinforced resin materials is expanding to achieve further weight reduction.
For example, polypropylene has excellent mechanical property balance and moldability. Its low specific gravity makes it ideal for automotive interiors and electrical components. Japan Polypropylene, a member of the Mitsubishi Chemical Group, has developed FUNCSTER™ Long Glass Fiber-Reinforced Polypropylene (LGF-PP) with innovative long-glass-fiber manufacturing technology. FUNCSTER™ has achieved high rigidity and can lightweight many module parts, offering unparalleled glass dissipation and seamless flow.
High heat-resistant carbon fiber-reinforced polyamide PYROFIL™ NT-C-40 is injection molded, producing highly rigid, strong, and lightweight parts. PYROFIL™ can create complex-shaped parts, increasingly being used as a substitute for metal parts as a resin material to accelerate vehicle weight reduction.
We have also developed DURABIO™, a recyclable, partially bio-based high-performance engineering plastic ideal for many automotive applications. This material is widely used in the interior and exterior parts of vehicles.
Manufacturing Study: Manufacturing techniques optimized for materials
Part manufacturers use various methods for automotive components. Casting and die casting are commonly used to produce metal parts, while injection molding is common when creating plastic parts. MCG CF SMC technology is used in an innovative manufacturing process to realize CASE materials.
For example, PP materials, such as high heat-resistant carbon fiber-reinforced polyamide PYROFIL™ pellet NT-C-40 and glass fiber-reinforced polypropylene FUNCSTER™, have excellent moldability for complex and large parts that are lightweight and have high rigidity, offering manufacturers a material advantage in injection molding.
The increasing importance of materials for reducing vehicle weight
The environment surrounding the automotive industry is expected to change dramatically as the shift to EVs continues against the backdrop of global environmental issues and other factors. Under such circumstances, it will become increasingly important to reduce the vehicle weight further to ensure long-distance cruising that uses less energy. As introduced in this report, the development of materials and the introduction of manufacturing methods are indispensable for vehicle weight reduction, and higher technological capabilities are required than ever before. Mitsubishi Chemical will contribute to the global environment and society by researching and developing various materials that will support the future automotive parts manufacturers.