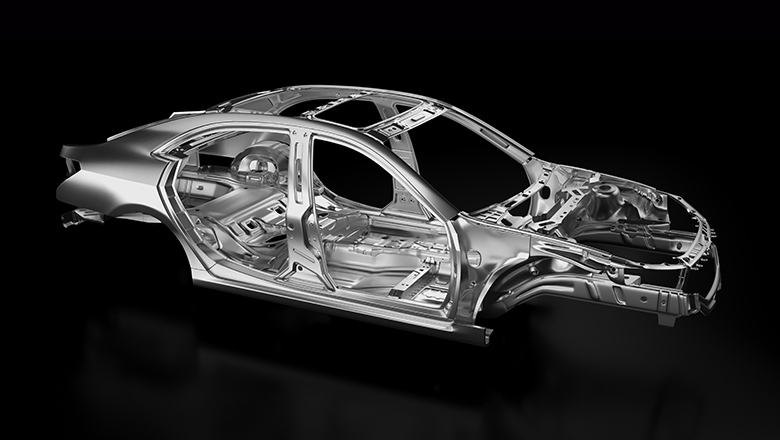
自動車産業と関わりの深い環境問題
これまで自動車メーカー各社は、地球温暖化の要因となるCO2の排出量を低減するさまざまな技術を開発し、HV(ハイブリッド自動車)やPHV(プラグインハイブリッド自動車)などを市場に投入してきました。
しかし、環境省が公開している「2020 年度(令和2年度)の温室効果ガス排出量(確報値)について」によると、2019年度のCO2総排出量のうち17.7%が運輸部門にあたり、この大部分が自動車からの排出となっています。
自動車が地球温暖化に与える影響は大きく、これまで以上にCO2排出量を抑えるための取り組みが求められているのです。
こうした動きがあるのは、もちろん日本だけではありません。世界各国の自動車におけるCO2排出量削減に向けた取り組みについて紹介します。最も厳しい規制を実施しているのはヨーロッパで、2021年時点で自動車の走行距離1KmあたりのCO2排出量を95gとする目標を設定し取り組み、2025年には70g程度まで削減することを目指しています。次いで厳しい規制を設けているのはアメリカで、2025年時点で89g/Kmを目標としています。
一方、アジアでは、日本が2020年時点で114g/Km、中国が116g/Km、インドが2021年時点で113g/Kmを目標にCO2の排出規制に取り組んできました。
参考:https://www.pwc.com/jp/ja/knowledge/thoughtleadership/automotive-insight/vol4.html
CO2排出量の低減に向けた自動車産業の取組事例
では、これまで以上にCO2排出量を低減するために、自動車産業全体ではどのような取り組みが行われているのか、3つの代表的な例を紹介しましょう。
EV・HVなどの開発
象徴的な取り組みとして挙げられるのが、EVやHVの開発です。すでにHVは世の中にも広く浸透し、軽自動車から大型車まで低燃費で静寂性も高いHVを選ぶユーザーは少なくありません。また、HVよりもさらに環境に優しいEVの注目度も高まっており、市販車も続々と登場しています。
走行中にCO2を一切排出しないEVは、エコカーの理想的な姿ともいえます。しかし、ガソリン車やHVに比べて巡航距離の短さが課題となっており、バッテリーの高性能化はもちろんのこと、車体の軽量化も求められています。
ガソリン車の燃費向上
EVやHVのニーズが急速に拡大している一方で、車体価格が比較的安価なガソリン車も根強い人気を誇っています。軽自動車やコンパクトカーを中心に、HVに負けないほどの低燃費を実現しているガソリン車も多く、CO2排出量が大幅に抑えられています。
また、ミニバンやSUVといった大型車は、エンジンのサイズも大きく大排気量の車種が一般的でしたが、最近ではエンジンのダウンサイジングがトレンドとなり低燃費化が進んでいます。
AI・IoTを活用した交通インフラの円滑化
社会全体でCO2排出量を抑えるためには、自動車そのものの技術開発だけでなく、交通インフラの円滑化も重要なポイントといえます。例えば、毎日のように激しい渋滞が発生していると、長時間のアイドリングによって無駄なCO2が排出されてしまいます。
そこで、このような慢性的な渋滞を解消するために、AIやIoTといった最先端技術を活用し交通インフラを円滑化するシステムが注目されています。機械学習によって渋滞が発生する区間を予測できれば、それを回避したルートを選択できるようになり、交通渋滞が緩和されCO2排出量の削減に貢献できるでしょう。
自動車の燃費向上を実現する技術・手法とは
CO2の排出量を抑制するためには、いかに少ない燃料で効率的に走行できるか、すなわち自動車の低燃費化が重要なカギとなります。低燃費化を実現するためには、エンジンだけでなく自動車全体の設計を見直すケースも少なくありません。
具体的にどのような技術や手法で自動車の低燃費化は実現されているのか、代表的な5つを紹介しましょう。
車体の軽量化
車体の剛性を確保しつつも、構造を見直すことで無駄なパーツや部分をなくし軽量化を実現する 同じ形状、サイズでも軽量な材料に変更することで軽量化を実現する
エンジン回りの改良
点火技術や燃料噴射の方法を変え、エンジン燃焼効率を改善することで、燃焼時に動力に変換されないエネルギーを低減する エンジンに高圧縮の空気を送り込むターボチャージャーを採用し、少ない排気量で大きなパワーを得る
駆動系の改善
ドライブシャフトなどの摩擦係数を低減することで、エンジンからのエネルギー損失を抑制 AT多段化により回転数の変化を抑え、燃焼効率を向上 無段変速機(CVT)はATよりもエネルギー損失が少なく、燃費も向上
転がり抵抗低減
タイヤ表面形状(トレッドパターン)を見直すことにより、転がり抵抗(摩擦)を抑制し低燃費化を実現
空気抵抗低減
流体力学をもとにボディ形状を改良することで、走行中の空気抵抗が低減され低燃費化を実現
自動車の軽量化をさらに加速する素材選びと素材に合わせた製法の検討
これらの中でも自動車の低燃費化を実現するためには、車体の軽量化が重要です。一つひとつのパーツの強度を保ちながら小型化・軽量化するには、材料と製法がポイントになります。材料選びや製法において、具体的にどのようなことが求められているのでしょうか。3つの具体例を紹介しましょう。
材料1:高張力鋼板(ハイテン)からアルミ、そしてマグネシウムへのシフト
自動車の構造材には以前より、強度や成形性、 表面処理性、そして価格面で優れた鉄鋼が多く使われてきました。鉄鋼の中でも炭素やニッケル、シリコン、マンガンなどの元素をごく微量に添加し 、組織制御によって強度を高めた高張力鋼板(ハイテン)、強度をさらに高めた超高張力鋼板(ウルトラハイテン)を自動車のセンターピラーやフロントピラー、サイドルーフレール、フロントルーフレールなど、自動車の骨格部材(構造材)に採用することで、これらの部材を薄肉化し、自動車の軽量化が図られてきたのです。
ハイテンやウルトラハイテンが自動車の骨格部材として使われてきたのに対し、シリンダーなどのエンジン部材、バンパービームやドア、ルーフなどの外板の材料では、鉄よりもさらに軽いアルミも使用比率が高まっています。
そして、現在では「実用金属中、最も軽い」とされるマグネシウムの利用も拡大しています。マグネシウムは航空機やロケットなどにも採用されるほど強度に優れ、信頼性の高い材料です。自動車部品のなかでは、燃料タンクやトランスミッション、ブラケット、シートフレームなどに採用されることも少なくありません。
マグネシウムはアルミよりさらに軽量で、実際にアルミニウムからマグネシウムに切り替えることで部品の重量を4分の1から3分の1程度に抑えられる可能性があります。
ちなみに、マグネシウムはもともと、可燃性が高く腐食しやすいといった欠点がありますが、アルミニウムや亜鉛といった金属を組み合わせたマグネシウム合金の開発により、これらの欠点を克服しています。
材料2:軽量な樹脂(プラスチック)材料の活用
一方、ハイテンやアルミ、マグネシウムなどの金属材料を、より軽量な樹脂に置き替える動きも顕著です。三菱ケミカルグループでは高機能な樹脂材料を開発し、内装部品などを金属から樹脂に置き換えることで自動車の軽量化に貢献しています。すでに、内装部品であるインパネコアや、機能部品のモーターハウジングを中心に、樹脂材料が活用されており、さらなる軽量化を実現するための特殊繊維強化樹脂材料の採用も拡大しています。
例えば、ポリプロピレンは機械物性バランス、成形性に優れて、低比重であることから自動車用の内装部品や電装部品として最適です。三菱ケミカルグループの日本ポリプロでは長繊維ガラスの製造技術を応用し「ガラス長繊維強化ポリプロピレンFUNCSTER™」を開発。自動車の各種モジュール部品において高い剛性と軽量化を両立することに成功しました。
高剛性と軽量化を両立した「ガラス長繊維強化ポリプロピレンFUNCSTER™」
また、「高耐熱炭素繊維強化ポリアミドパイロフィル™ペレットNT-C-40」は、通常の射出成型で高剛性・高強度・軽量な自動車部品を製造できる材料です。複雑形状の部品も簡単に製造でき、自動車の軽量化を促進する樹脂材料として金属部品の代替品での利用も進んでいます。
さらに、再資源化が可能なバイオプラスチックとして「植物由来/環境適合性高機能エンジニアリングプラスチック DURABIO™」も開発し、自動車内外装部品に広く採用されています。
製法:素材に合わせた製法の検討
※FMC:Forged Molding Compound、SMC:Sheet Molding Compound
自動車部品の製造にはさまざまな方法が用いられています。金属部品の製造には鋳物やダイキャスト、プラスチック部品の製造には射出成型などの製法が用いられるのが一般的です。
例えば、特殊繊維強化樹脂(プラスチック)材料として紹介した「高耐熱炭素繊維強化ポリアミドパイロフィル™ペレットNT-C-40」をはじめ、「ガラス長繊維強化ポリプロピレンFUNCSTER™」等のPP材料は成型性に優れ、複雑で大型な部品も射出成型で軽量・高剛性な部品を量産できるメリットがあります。
自動車の軽量化を実現する「素材」の重要性はさらに高まる
地球環境問題への対応などを背景に今後、EVへのシフトがさらに進み、自動車産業を取り巻く環境は大きく変化していくと考えられます。そうした中、より少ないエネルギーで長距離を巡航するためには自動車そのもののさらなる軽量化がますます重要になります。今回ご紹介したように、自動車の軽量化には材料の開発や製法の検討が不可欠であり、これまで以上に高い技術力が求められます。三菱ケミカルでは、将来の自動車産業を支えるさまざまな材料を研究・開発し、地球環境と社会に貢献していきます。